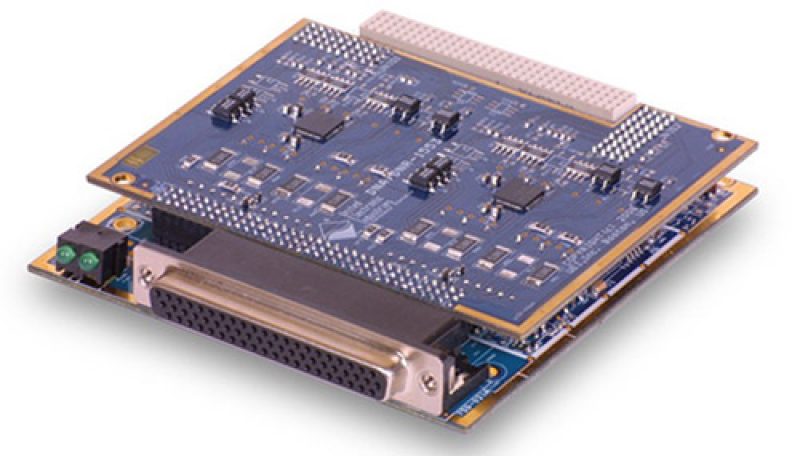
Dual Channel MIL-STD-1553 interface board
DNx-1553-553
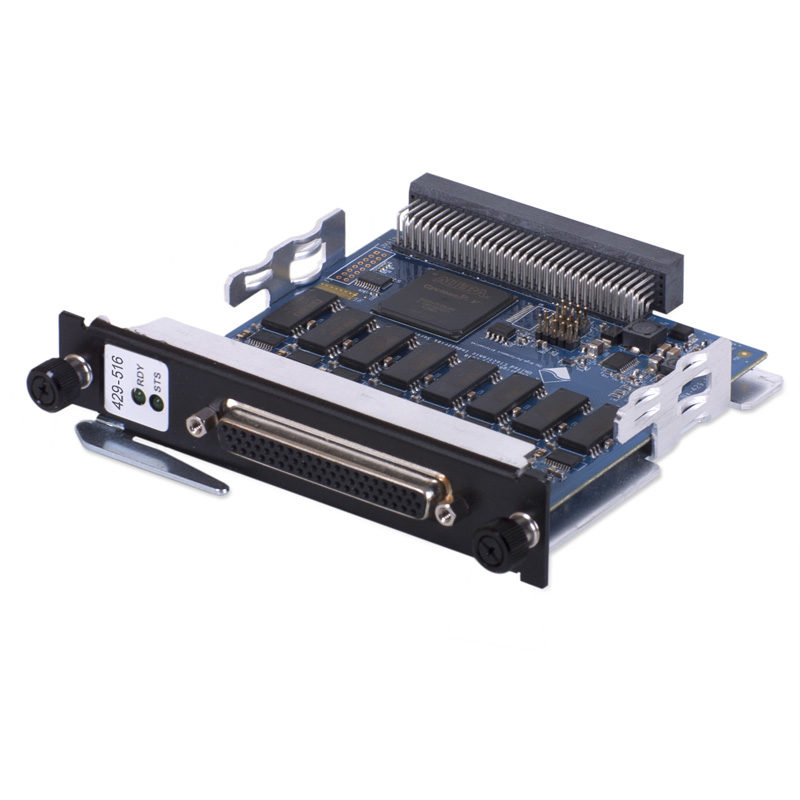
24-channel ARINC 429 Interface
DNx-429-516-024
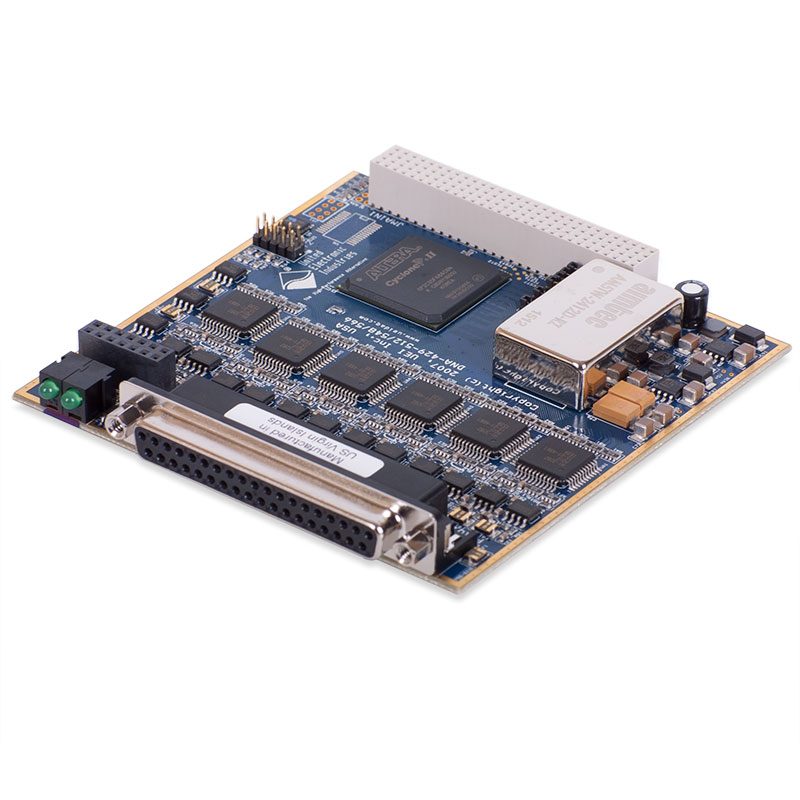
ARINC 429 Interface board with 6 TX and 6 RX channels
DNx-429-566
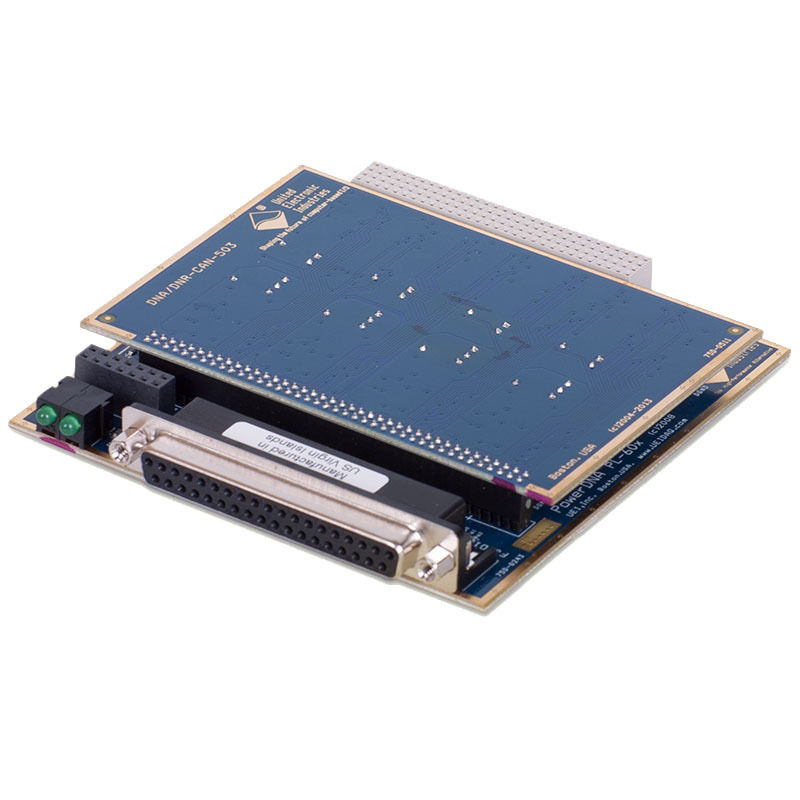
4-port, CAN bus interface board
DNx-CAN-503
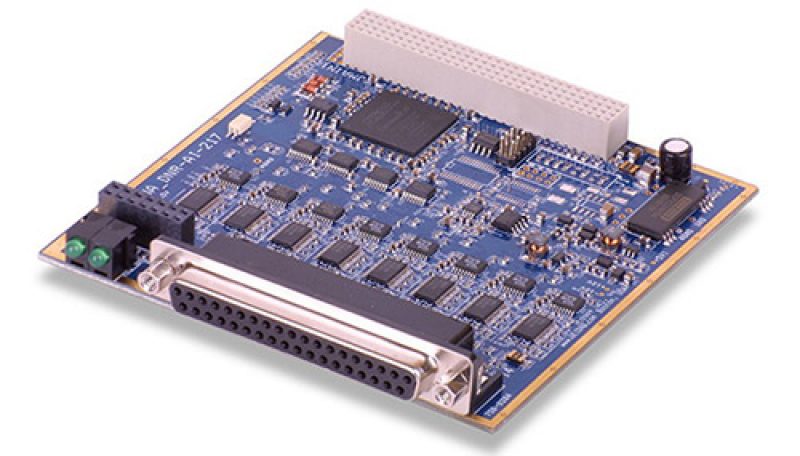
16-Channel, 24-bit 120 kS/s high-speed simultaneously sampling A/D board
DNx-AI-217
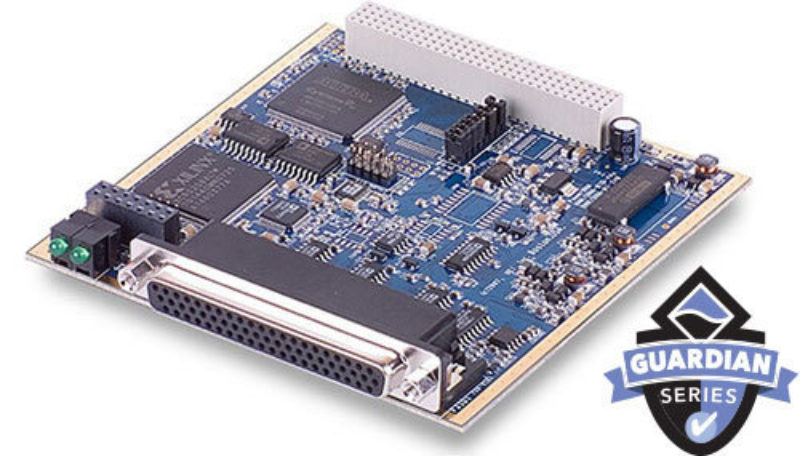
48-Channel digital input board with voltage monitoring
DNx-DIO-448
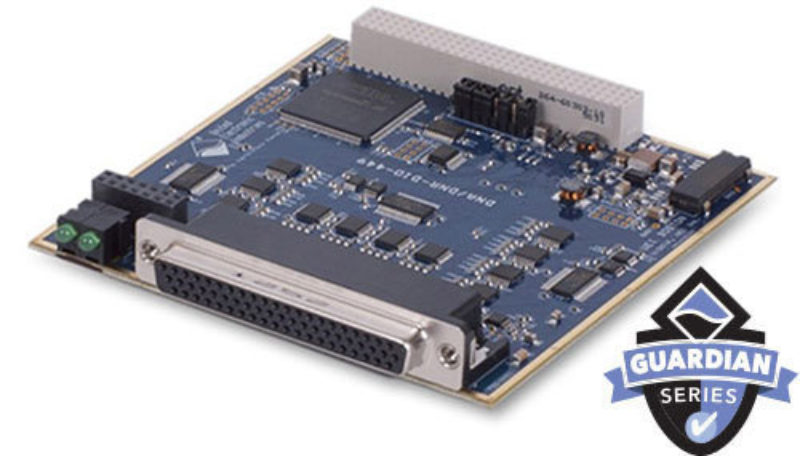
48-Channel 0-150V AC/DC digital input board with voltage monitoring and self test
DNx-DIO-449
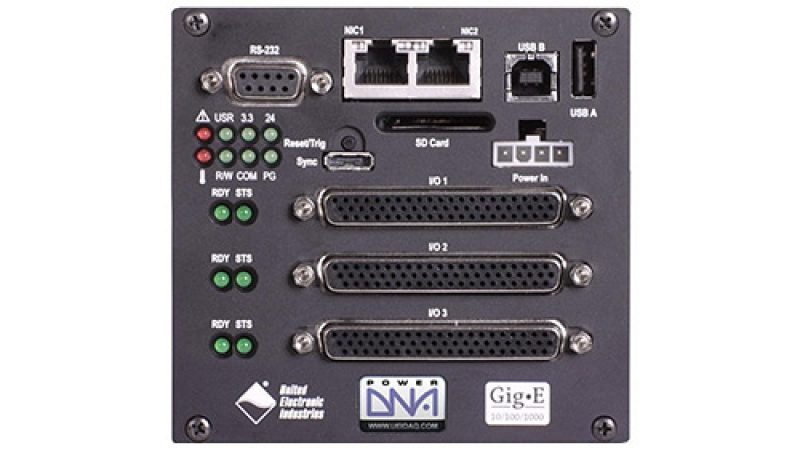
Real-Time, GigE, Programmable Automation Controller (PAC) with 3 I/O slots
UEIPAC 300-1G