Your application has a lot of requirements. It needs to process an array of data signals, reliably operate in challenging environments and do so in a very tight space. What do you do?
We’ve got a solution. Our new rugged MF-102 Multifunction I/O board is packed with features and updated options making it the ideal fit for a variety of applications like automotive and airborne systems as well as a crucial COTS component of the Ground Combat Systems Common Infrastructure Architecture (GCIA) framework for military vehicles.
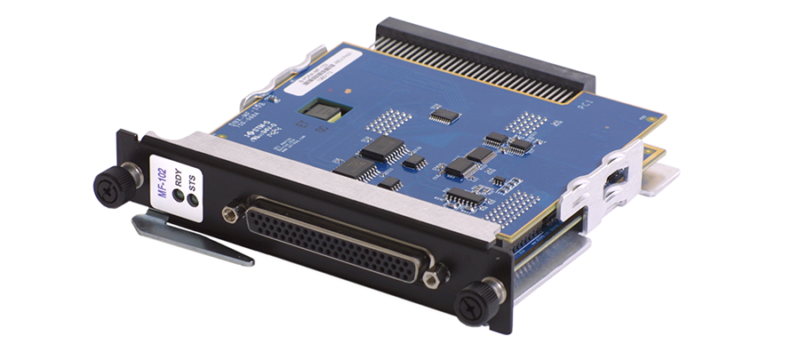
For a deeper dive into this board’s capabilities, we sat down with Sean Foley, UEI’s Senior Embedded Hardware Engineer. Sean was responsible for the hardware development of the MF-102 including schematic design, PCB layout, and FPGA logic. He also worked on troubleshooting with the software development and design verification teams.
Q: What is the MF-102 Multifunction board?
A: The multi-function board is a multiple sub-system, high density DAQ system. It has 16 SE or 8 Diff analog inputs, 2 analog outputs, 16 digital inputs or outputs, RS-232/485, TTL lines, and 2 isolated CAN channels. It gives a lot of flexibility in a small package which is very important in the lower board count chassis, especially the new DNR-MIL-4 Military Grade Chassis.
Q: It looks like an updated version of our MF-101 Multifunction Board. Why the update and how has the MF-102 been updated or “improved”?
A: Actually, it's less of an update and more of an alternate option. Instead of giving the user an I2C channel we give them 2 CAN channels. One interesting thing about the development of the MF-102 is we took the MF-101 Multifunction Board, removed the serial, I2C, and TTL sub-systems. This gave us enough room to fit 3 connectors that would connect to a daughter board. This means the base board has the core Ain, Aout, Din and Dout, but the daughter board can add whatever flexibility is needed.
On the MF-102 the daughter board has a TTL, Serial, and CAN (this was the customer demand) but we can easily develop new daughter boards in the future to have different sub-systems instead.
This, once again, helps us market systems like the MIL-4 that are slot prohibitive. You can pick 3 boards you really need and then use a MF-101 or MF-102 to fill the rest of the requirement.
Q: What are the intended uses / industries / applications?
A: Going back to the flexibility and density point I mentioned before, this board is going to do well in embedded applications. There is nothing stopping you from getting similar functionality using 5 or 6 existing UEI boards, but if you're looking to use a small form factor with a low power budget, the MF-102 is going to help you get that done. Given it provides a large range of DAQ I/O and also two CAN channels it will be well suited for the MIL vehicle market (what it was designed for).
Q: What can it do that other UEI I/O boards or competitor boards can’t?
A: MF-102 fits the I/O it provides in a rugged and small form factor. This is what it does that the other UEI or competitors boards can’t. If you need similar I/O, customers would have to go with a multi-board or custom solution.
As you can see the MF-102 Multifunction board provides you with a lot of options. The high voltage range (±80 V) makes it “an ideal measurement solution for automotive, aerospace and power generation applications." And the inclusion of high-speed CAN Bus ports presents the perfect embedded I/O solution for military ground-vehicles as well as next generation aircraft that use ARINC-825 avionic standard.
Got Questions? Our customer support staff has the answers